Energy consumption and efficiency factors associated with non-woven machinery are influenced by various aspects of the production process:
- Machine Type and Configuration: Different types of non-woven machinery (spunbond, meltblown, airlaid, etc.) have varying energy requirements based on their operational principles and configurations.
- Process Parameters: Adjusting process parameters such as temperature, pressure, speed, and tension affects energy consumption. Optimizing these parameters for efficiency without compromising fabric quality is crucial.
- Material Selection: The choice of raw materials, including fibers or polymers, impacts energy consumption during processing. Using recycled or sustainable materials might reduce energy inputs.
- Heating and Cooling Systems: Machinery components requiring heating or cooling, such as meltblown extruders or thermal bonding units, consume significant energy. Efficient systems help minimize wastage.
- Automation and Control Systems: Advanced control systems and automation technologies optimize energy usage by ensuring machinery operates at optimal levels and reduces idle time.
- Energy Recovery Systems: Implementing energy recovery systems that capture and reuse heat or other forms of energy generated during production processes can improve overall efficiency.
- Maintenance Practices: Regular maintenance ensures machinery operates at peak efficiency, reducing energy wastage due to equipment malfunctions or suboptimal performance.
- New Technology Integration: Upgrading machinery with newer, more energy-efficient technologies or components can significantly reduce energy consumption.
- Process Integration and Optimization: Integrating different processes or combining steps within a single machine setup can streamline production, reducing energy consumption by minimizing unnecessary movements or stages.
- Industry Standards and Regulations: Adherence to energy efficiency standards and compliance with regulations encourage the use of more energy-efficient machinery and practices.
Efforts to improve energy efficiency in non-woven machinery not only reduce operational costs but also align with sustainability goals, nonwoven machines reducing the environmental impact associated with fabric production. Manufacturers continually seek ways to optimize energy usage while maintaining or enhancing the quality and output of non-woven fabrics.
How does non-woven machinery ensure consistency and uniformity in fabric production?
Non-woven machinery employs various mechanisms and processes to ensure consistency and uniformity in fabric production:
- Precise Control Parameters: Machinery is equipped with controls for regulating factors like speed, tension, temperature, and pressure, ensuring consistency in fabric characteristics.
- Advanced Technology Integration: Modern non-woven machinery incorporates advanced technologies, such as automation, digital controls, and sensors, to monitor and adjust production parameters in real-time for uniform output.
- Process Stability: Machinery is designed to maintain stable processing conditions throughout the production line, minimizing fluctuations that could impact fabric quality.
- Fiber Preparation: Processes like carding or opening ensure fibers are aligned and evenly distributed before web formation, enhancing uniformity in the fabric structure.
- Web Formation Techniques: Machinery uses various web formation techniques (such as airlaid, spunbond, or meltblown) designed to create consistent fiber arrangements and densities, ensuring uniformity in fabric properties.
- Bonding Methods: Different bonding methods like thermal bonding, needle punching, or chemical bonding ensure consistent fiber entanglement or adhesion, leading to uniform fabric strength and integrity.
- Quality Control Systems: Machinery incorporates quality control systems that monitor and adjust production parameters based on set criteria, ensuring consistent fabric characteristics and detecting deviations.
- Standardized Processes: Non-woven machinery follows standardized processes and operating procedures, minimizing variations and deviations in fabric production.
- Sampling and Testing Protocols: Regular sampling and testing of fabrics during production help maintain quality standards, identifying any deviations early for corrective action.
- Operator Training and Expertise: Well-trained operators understand the machinery’s capabilities and parameters, ensuring consistent operation and making necessary adjustments for uniform fabric output.
By employing these measures and technologies, non-woven machinery ensures that fabrics produced exhibit consistent properties, such as weight, thickness, strength, porosity, and surface characteristics, meeting industry standards and customer specifications.
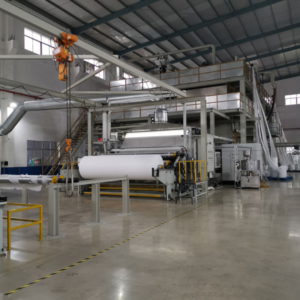