Silicone couplers are flexible connectors made from silicone material that are used to connect two pipes or tubes together. They are commonly used in automotive and industrial applications, as well as in medical and scientific fields. Silicone couplers are designed to provide a high level of flexibility and resistance to high temperatures, making them ideal for applications where heat and movement are a concern.
Some common features and applications of silicone couplers include:
High temperature resistance: Silicone couplers are designed to withstand high temperatures, making them ideal for use in high-performance engines and other applications where heat is a concern.
Flexibility: Silicone couplers are flexible and can be bent or twisted to fit into tight spaces, making them ideal for use in applications where space is limited.
Resistance to chemicals and oils: Silicone couplers are resistant to many chemicals and oils, which makes them a popular choice in the automotive and industrial sectors.
Medical and scientific applications: Silicone couplers are used in medical devices and scientific equipment, such as laboratory tubing and catheter connectors.
Automotive applications: Silicone couplers are commonly used in automotive applications, such as turbocharger systems, intercooler piping, and air intake systems.
Industrial applications: Silicone couplers are used in industrial applications, such as chemical processing, food and beverage production, and pharmaceutical manufacturing.
When selecting silicone couplers, it’s important to consider factors such as the diameter and length of the coupler, as well as the intended application and operating conditions. Silicone Coupler supplier It’s also important to choose a high-quality product from a reputable supplier to ensure reliable and safe performance.
What are some reputable suppliers of silicone couplers?
There are many reputable suppliers of silicone couplers that can be found online or in specialty automotive stores. Here are a few examples:
Mishimoto: Mishimoto is a well-known supplier of high-performance automotive parts, including silicone couplers. Their couplers are made from high-quality materials and are designed to withstand high temperatures and pressures.
Vibrant Performance: Vibrant Performance is another well-known supplier of performance automotive parts, including silicone couplers. Their couplers are available in a variety of sizes and colors, and are designed to fit a wide range of applications.
HPS Performance Products: HPS Performance Products is a leading supplier of silicone couplers and other high-performance automotive parts. Their couplers are made from high-quality materials and are available in a range of colors and sizes.
TurboHoses: TurboHoses is a supplier of silicone couplers and other performance parts for turbocharged engines. Their couplers are designed to withstand high boost pressures and temperatures, and are available in a variety of sizes and colors.
Pegasus Auto Racing Supplies: Pegasus Auto Racing Supplies is a supplier of racing and performance parts, including silicone couplers. Their couplers are made from high-quality materials and are designed to meet the demands of high-performance applications.
These are just a few examples of reputable suppliers of silicone couplers. It’s always a good idea to do your own research and compare prices and product specifications before making a purchase.
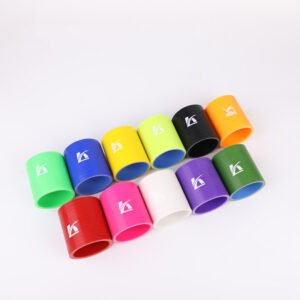